Tension spring clamps are indispensable components in various industrial and mechanical sectors, playing a crucial role in applications ranging from automotive assembly to electronic device manufacturing. These devices are specifically engineered to harness the restorative force of springs, providing a secure grip and stabilization under tension. Understanding their functional dynamics and selection criteria can significantly enhance operational efficiency and product longevity in diverse applications.
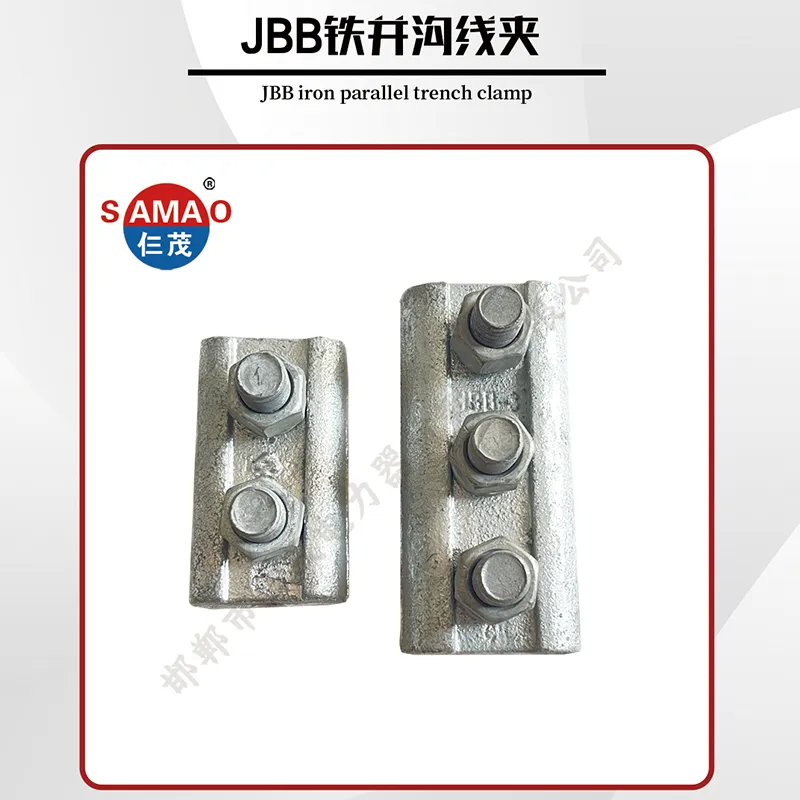
Tension spring clamps exemplify the harmonious blend of simplicity and effectiveness. Unlike conventional clamping devices, tension spring clamps utilize the mechanical force stored in coiled springs to exert consistent pressure, ensuring materials are held tightly together. This makes them especially valuable in environments where fluctuating forces or movements are expected, as the clamping force can be automatically adjusted through the spring’s elasticity without manual intervention.
Choosing the right tension spring clamp involves assessing several key factors. Material composition is paramount; these clamps are typically crafted from stainless steel for corrosion resistance or carbon steel for enhanced strength. The choice between these materials depends on the operating environment and specific usage requirements—stainless steel for high-moisture settings like marine hardware applications, while carbon steel might be chosen for heavy-duty industrial contexts.
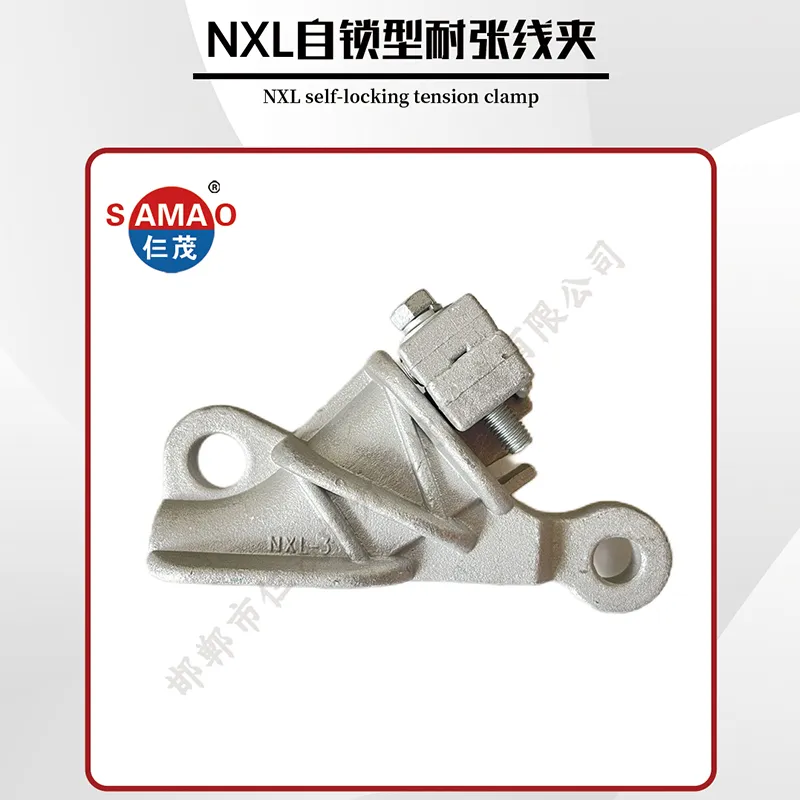
The diversity in design is another crucial consideration. Various models are engineered to cater to specific functions; for instance, some have extended loops offering a wider range of motion, ideal for applications in robotics where precision and flexibility are paramount. Others might feature reinforced coils to withstand higher pressures, suitable for automotive assembly lines where robust, unfailing performance is critical.
Implementing tension spring clamps effectively requires an understanding of precise load requirements and application settings. In scenarios where delicate components are involved, opting for a clamp with adjustable tension control ensures minimal risk of over-compression and potential damage. This ability to fine-tune the force exerted is what gives tension spring clamps an edge in meticulous operations such as those in electronic circuit systems.
tension spring clamps
From an operational perspective, tension spring clamps offer remarkable durability and lifespan compared to alternative fastening solutions. Their maintenance is straightforward, primarily involving periodic inspection for signs of wear on the spring mechanism and ensuring the integrity of the clamp’s grip remains intact. This simplicity in maintenance, combined with their inherent reliability, translates into reduced downtime and operational costs over the long term.
The environmental adaptability of tension spring clamps also complements their broad utility. They maintain functionality across a wide temperature range, making them viable for use in extreme conditions such as aerospace or refrigeration industries. Their design accommodates vibrations and dynamic loads, ensuring consistent performance whether in the high turbulence of an aircraft or the gentle pulsations of a manufacturing line.
Moreover, the integration of tension spring clamps in safety-critical systems illustrates their indispensable value. In automotive applications, for example, they secure pivotal components that must endure continuous stress while maintaining precise positioning. In such contexts, the reliability of tension spring clamps becomes synonymous with safety and operational excellence.
For professionals in manufacturing and engineering sectors, understanding these facets of tension spring clamps—material selection, design variations, operational adaptability, and maintenance—is pivotal. Leveraging this knowledge empowers informed decision-making, ultimately leading to enhanced product performance and reliability.
In conclusion, tension spring clamps are not merely auxiliary tools but are central to the structural integrity and efficiency of modern manufacturing systems. Their unique capability to combine strength, adaptability, and reliability makes them indispensable across numerous industries. As technology progresses, refining the design and application of these clamps continues to offer potential for even greater innovation and functionality, solidifying their role as a cornerstone component in engineering solutions.