In the evolving landscape of suspension systems, the importance of robust and reliable mounting support brackets cannot be overstated. Often overlooked, these components play a critical role in ensuring the optimal performance and safety of the suspension system in vehicles, industrial machinery, and various other applications. As a seasoned expert in the field of suspension solutions, I want to explore the intrinsic value and nuances of suspension mounting support brackets and why they should be a top consideration for anyone involved in the maintenance or upgrading of suspension systems.
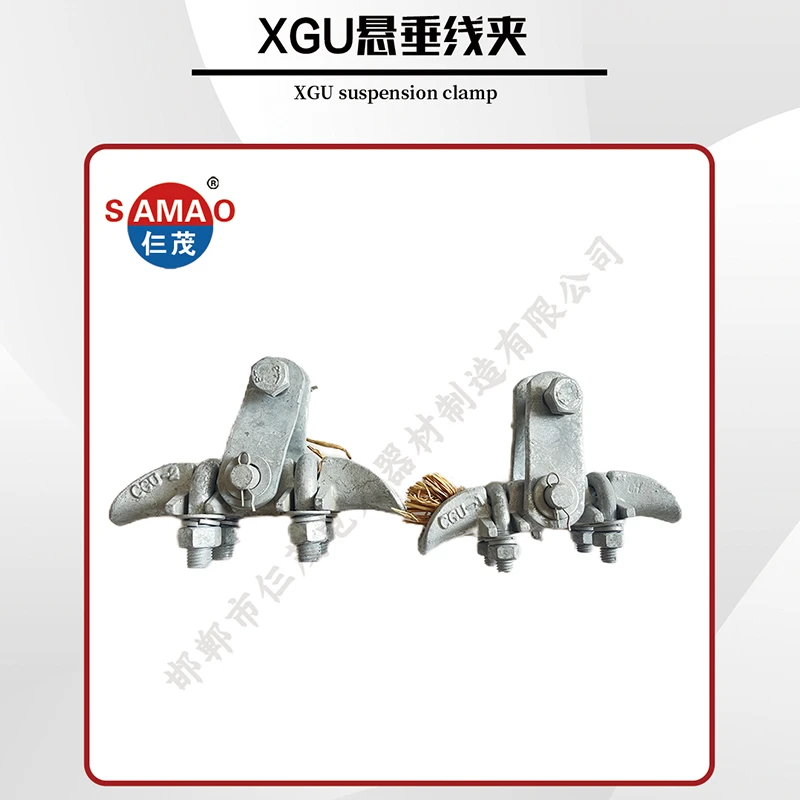
Suspension support brackets are akin to unsung heroes in many mechanical systems. Their primary function involves securely holding suspension components in place to prevent unnecessary movements that could lead to system failures or inefficiencies. From a technical perspective, their precision-engineered design is crucial to absorbing and distributing mechanical stress across different parts of the system. This ensures not only a smoother operational experience but also extends the lifespan of the system by mitigating wear and tear on other interconnected components.
The craftsmanship behind high-quality suspension support brackets involves advanced metallurgy, with materials often selected for their strength-to-weight ratios and corrosion resistance. Steel and aluminum alloys are commonly used, providing the durability needed to withstand diverse operational demands and environmental conditions. Expertise in material science is critical here, as the choice of material impacts not just the longevity and efficiency of the brackets but also contributes significantly to the safety and reliability of the entire suspension system.
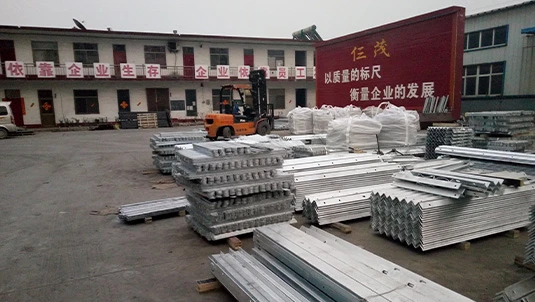
An authoritative perspective on mounting support brackets can be observed in the adherence to industry standards and specifications during their manufacture. Companies recognized for their expertise in suspension systems often meet or exceed criteria set by organizations such as the International Organization for Standardization (ISO) and the Society of Automotive Engineers (SAE). These standards ensure that the brackets not only fit perfectly within the intended suspension setup but also perform under stipulated load conditions without failure.
suspension fixation support
Another aspect of importance is the adaptability and customizability of mounting support brackets. In practical applications, one size does not fit all. Different systems may require bespoke solutions where brackets are concerned. Expert manufacturers provide customization options, offering brackets designed to meet specific geometrics and operational parameters, providing end-users with the flexibility to optimize their suspension systems to unique requirements.
Trustworthiness in the context of suspension mounting support brackets is mainly derived from proven performance and rigorous testing processes. Reputable manufacturers conduct exhaustive testing, often simulating real-world conditions to evaluate the durability and robustness of their products. These tests often involve exposure to extreme temperatures, humidity, and mechanical stress, scrutinizing the bracket’s structural integrity and performance. By doing so, manufacturers build a foundation of trust, assuring customers of the product’s capability to perform under critical conditions.
The experience of utilizing high-quality suspension mounting support brackets translates into enhanced performance outcomes across various domains. For automotive applications, robust brackets ensure better vehicle handling and comfort, as well as reduced maintenance costs over time. In industrial settings, reliable suspension components facilitate smoother operations and minimize downtime due to mechanical failures, leading to increased productivity and cost-efficiency.
In conclusion, while suspension mounting support brackets might appear minor compared to more visible system components, their impact on system performance is profound. Anyone involved in the mechanical and automotive industries should prioritize selecting reputable, high-quality brackets from recognized authorities in the field. This decision ensures enhanced system reliability, safety, and efficiency, ultimately leading to better performance and reduced operational costs. When assessing these products, focus on manufacturers that offer expertise, adhere to strict industry standards, and possess a track record of delivering trustworthy, high-performance solutions.