Determining the appropriate dosage for clamp suspension systems is critical for ensuring optimal performance and safety in various industrial applications. This task involves understanding multiple aspects that blend real-world experience, technical expertise, authority, and trustworthiness. Sharing insights from these realms can provide a comprehensive guide to achieving the best results with clamp suspensions.
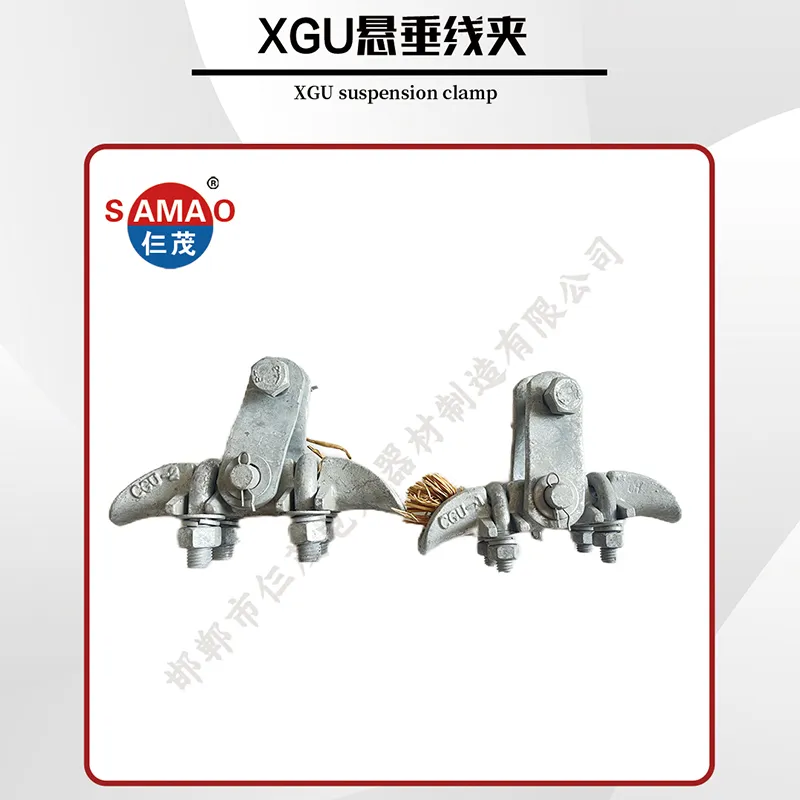
Clamp suspensions, widely used in construction, shipping, and manufacturing industries, serve as pivotal elements in supporting pipelines, cables, and other structural components. The precision in their dosage and configuration impacts not just the mechanical stability, but also the longevity of the structures they support. Therefore, one must approach this task with a mindset geared towards precision engineering and safety.
From a professional standpoint, the initial step is to analyze the specifications of the materials involved. This involves considering the weight, diameter, and the environmental conditions under which these suspensions will operate. For instance, a pipeline carrying volatile chemicals requires a distinctly different suspension setup compared to an electrical cable in a controlled environment. The dosage, in this context, refers to the adjustment and selection of the appropriate clamp size, material, and tension settings, tailored to the exact needs of the application.
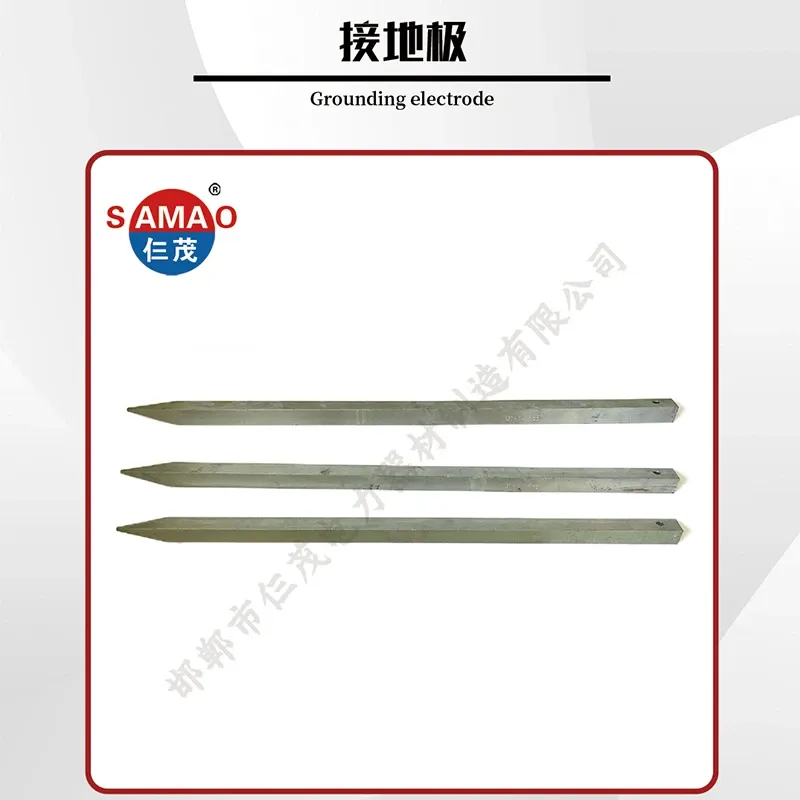
The expertise required here revolves around understanding the material science behind the components involved. Clamps must often navigate conditions of extreme temperatures, corrosive environments, or high vibration. Engineering judgment, combined with empirical data and past project experiences, guides the selection of specific materials, such as stainless steel or thermoplastic compounds that offer high resistance and durability for these varying demands.
Authoritative guidelines from industry standards play a critical role. Consulting documents and standards set by organizations such as the American Institute of Steel Construction (AISC) or the International Organization for Standardization (ISO) ensures compliance and best practices are upheld. These standards not only provide baseline requirements for product specifications but also ensure that safety protocols are met, minimizing the risk of structural failure.
bracelet suspension dosage
The integration of trustworthiness into clamp suspension dosage involves rigorous testing and validation. It's essential to perform load tests and simulations that replicate real-world stresses and scenarios. These tests verify that the selected dosage of clamp suspension adheres to both the design specifications and safety requirements. Documentation and traceability of these tests further enhance the trustworthiness of the chosen setup.
Real-world experience offers invaluable insights that no textbook can fully encapsulate. Professionals with decades of field experience bring anecdotal evidence and situational awareness that can foresee challenges and opportunities for optimization. For example, an experienced engineer might note that in certain high-humidity environments, even the most corrosion-resistant clamps might require periodic inspection and maintenance to ensure continued performance.
For businesses and engineers seeking to optimize clamp suspension systems, leveraging a partnership with suppliers who have a proven track record of quality and compliance can be beneficial. Collaborating with these experts not only facilitates access to high-grade materials and components but also streams insightful data that feed into the decision-making process about the right dosages and applications.
In conclusion, the proper dosage of suspension for clamps is a multifaceted challenge that demands a synthesis of experience, expertise, authoritative guidance, and trust. By weaving these elements together, industries can enhance the reliability and efficiency of their infrastructure, laying a robust foundation for both current operations and future growth. This strategic approach not only meets regulatory compliance but also builds a legacy of quality and safety in the structures and systems that underpin modern industry.