Navigating the realm of electrical components can often lead to discovering essential yet overlooked items like the dead end clamp. This unassuming device plays a critical role in electrical infrastructure, particularly in securing and terminating overhead power lines. Whether you're an industry professional or an enthusiast keen on understanding more about this indispensable tool, having the right knowledge about dead end clamps is crucial.
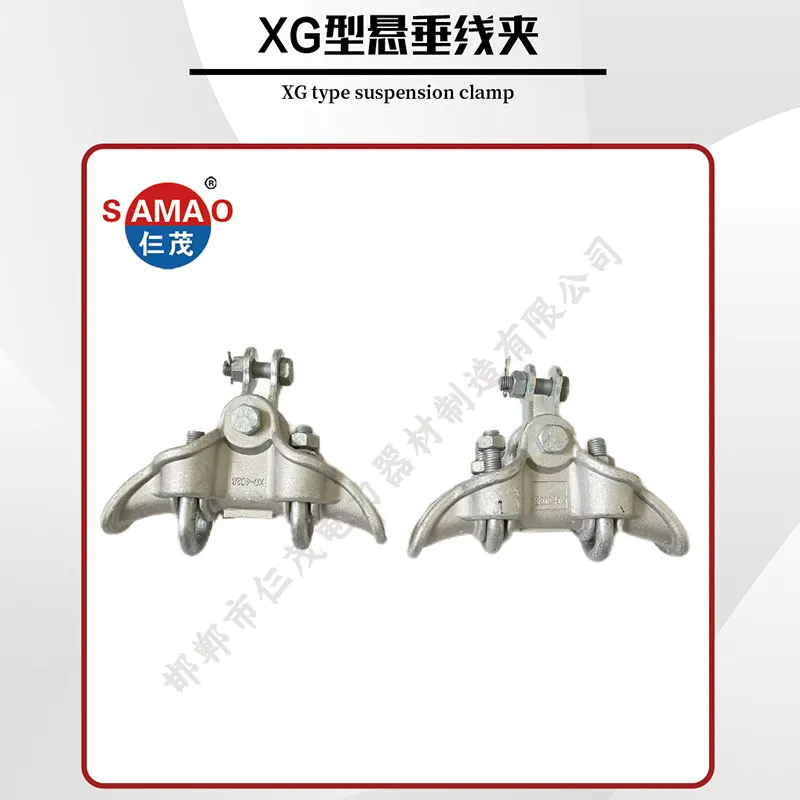
Dead end clamps, also known as line end clamps or overhead line clamps, are specifically designed to secure the conductor to an anchor point. They ensure the stability of power lines, preventing them from sagging or swaying excessively due to environmental factors like wind or ice accumulation. This function is vital for maintaining consistent electrical flow and safety in various settings, whether urban or rural.
The experience of working with dead end clamps highlights their ease of installation and robust performance. Most experienced technicians and linemen favor these clamps for their simplicity and efficiency, which minimizes downtime during installation or maintenance projects. The intuitive design typically features an adjustable jaw or mechanism that clamps onto the wire securely, ensuring a firm grip even under high tension. This adjustability means they can accommodate various conductor sizes, offering flexibility in diverse applications.
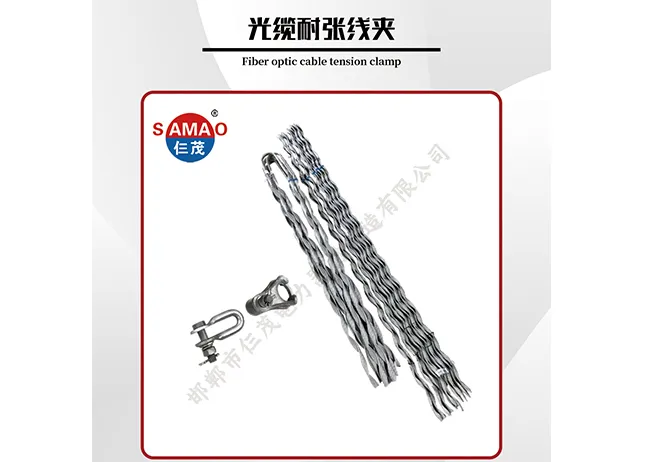
From an expertise standpoint, dead end clamps are engineered using materials designed to withstand high mechanical stress and varying environmental conditions. Common materials include aluminum alloys, stainless steel, or galvanized steel. Each material choice provides specific benefits; for instance, aluminum is lightweight and resistant to corrosion, while stainless steel offers superior strength and longevity.
Understanding these material properties is essential for choosing the right clamp for specific environmental circumstances.
dead end clamp
Moreover, the technology behind dead end clamps has evolved, with many manufacturers incorporating innovative features to enhance performance. Modern designs may include anti-theft features, vibration dampening components, or improved corrosion-resistant coatings. These advancements ensure that dead end clamps not only serve their primary function but also extend the life of the power lines and reduce maintenance costs.
In terms of authoritativeness, leading manufacturers often test their dead end clamps rigorously to adhere to international standards and certifications. Products boasting compliance with standards such as ISO 9001 or IEC ensure reliability and quality assurance, giving consumers confidence in their purchase. Moreover, industry bodies and electrical standards organizations frequently update best practices concerning these components, reflecting new research and technologies.
Trustworthiness in dead end clamp selection is bolstered by choosing reputable brands known for their quality and service. Brands with a track record of innovation and customer satisfaction often provide detailed technical specifications and support, ensuring that customers can make informed decisions. Reviews and case studies from verified customers provide additional assurance, highlighting real-world scenarios where these clamps have proven successful.
In conclusion, dead end clamps are vital components in electrical infrastructure, offering secure and stable solutions for terminating overhead power lines. Their reliable performance, ease of use, and technological advancements make them an indispensable tool for professionals in the field. By understanding the materials, innovations, and standards associated with dead end clamps, users can make informed choices that ensure long-lasting and effective solutions for their electrical projects. By prioritizing expertise, authoritativeness, and trustworthiness in their selection, consumers can leverage these components' full potential to enhance the safety and efficiency of their power line systems.