Plastic suspension clamps are revolutionizing various industries by providing a versatile and effective solution for managing wiring and cabling systems. Renowned for their lightweight yet durable construction, these clamps are becoming an essential part of modern infrastructure, particularly in sectors that require high reliability and efficiency such as telecommunication, automotive, and construction.
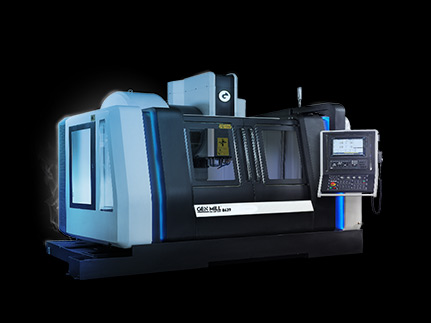
Experience demonstrates that the adaptability of plastic suspension clamps significantly contributes to their increasing popularity. Users across various fields have reported that these clamps not only withstand environmental stresses but also offer ease of installation, which reduces labor time and cost. A crucial advantage of using these clamps is their resistance to corrosion — unlike metal clamps, plastic variants are immune to rust and can maintain their integrity in harsh weather conditions, making them ideal for outdoor applications.
Expertise in the field indicates that plastic suspension clamps are an engineered product tailored to meet specific industry standards. They are designed using high-grade thermoplastics known for their strength and resilience. Polyamide and polypropylene are some of the most commonly used materials due to their excellent mechanical properties, such as high tensile strength and flexibility. Their design often includes features such as UV stabilization, which prevents degradation from sunlight exposure, thus ensuring longevity.
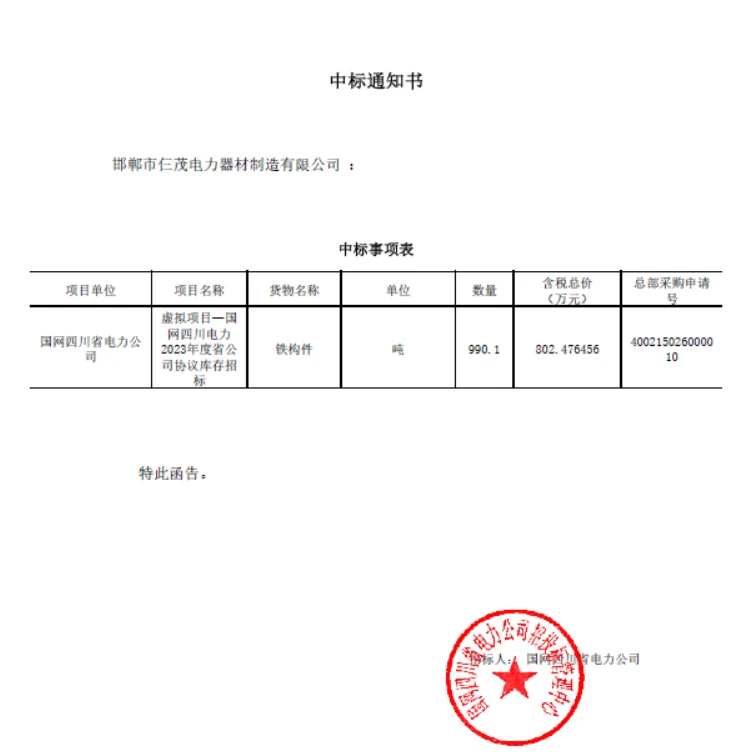
Authoritativeness in the manufacturing of plastic suspension clamps is governed by strict compliance with international standards. Manufacturers ensure that the products undergo rigorous testing to meet specifications for weight-bearing loads, thermal resistance, and electrical insulation. The assurance of these quality standards places plastic suspension clamps in a leading position in the market, providing reliability and safety — crucial elements for infrastructure projects.
Trustworthiness is another cornerstone of why these clamps are favored globally. Case studies from utility companies and infrastructure projects often highlight the reliability of plastic suspension clamps in field applications. Feedback from project managers and engineers consistently emphasizes their performance, citing their success in securing cables under varying environmental conditions without degradation or failure.
plastic suspension brackets
In practical applications, suspension clamps are often employed in pairs with messenger wires that bear the load of aerial cables. This setup minimizes sagging and maintains cable position over long distances. Their use in telecommunications, for example, is essential for maintaining signal integrity and ensuring uninterrupted service. This is especially important in rural or extreme environments where reliable infrastructure can significantly affect service delivery.
The automotive industry also capitalizes on the benefits of plastic suspension clamps. Within vehicle assemblies, these components help secure wiring harnesses, minimizing the risk of mechanical wear or short circuits due to vibrations or engine heat. The non-conductive nature of plastics helps ensure that there are no unintended electrical interferences, maintaining vehicle safety.
For construction applications, particularly in the installation of suspended ceilings and lighting systems, these clamps provide secure support and ease of adjustment, making them a preferred choice for contractors who value both efficiency and safety. The clamps' adaptability allows for repositioning without the need for significant structural modifications, leading to cost savings and reduced project timelines.
In conclusion, plastic suspension clamps are a product of notable expertise and engineering excellence. Their widespread application across multiple high-demand industries showcases their adaptability and reliability. Through continuous innovation and adherence to stringent industry standards, plastic suspension clamps remain a cornerstone in the modern management of wiring and cabling systems, appreciated for their authoritative quality and trusted performance. Emphasizing their multiple benefits, from corrosion resistance to ease of installation, ensures they hold their place as a widely favored component in the infrastructure sector.