Understanding the critical role of lifting clamps in sheet metal operations reveals the intricate balance between safety, efficiency, and precision in handling metallic materials. Often, these tools are the unsung heroes in many manufacturing settings, enhancing operations while safeguarding both personnel and products.
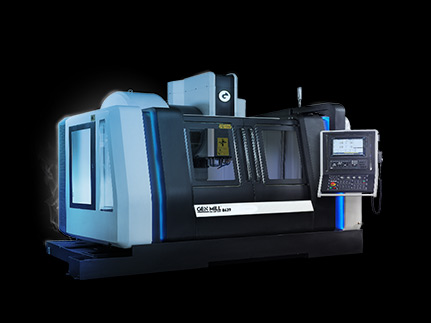
Lifting clamps, particularly those designed for sheet metal, facilitate the secure transfer and maneuvering of sheets without risking deformation or damage. The expertise inherent in operating these clamps is not merely an added advantage but a necessity for optimal productivity and safety in the workplace.
First and foremost,
the expertise involved in selecting the right lifting clamps is crucial. Factors such as the weight, thickness, and surface finish of the sheet metal determine the most suitable clamp type. For instance, vertical lifting clamps, with their robust construction, are suitable for lifting hefty steel plates, whereas horizontal clamps provide stable transfer of thinner sheets, preventing unnecessary bending or slipping.
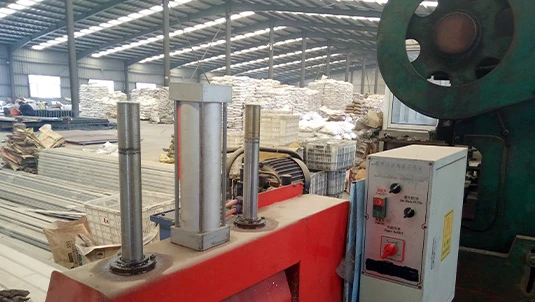
Manufacturers like Magswitch, CM, and Crosby Ironside have cultivated a reputation of authority in producing reliable lifting clamps, verified by their wide usage across various industries. Their dedication to quality and innovation reinforces the trustworthiness of these tools, making them indispensable in high-stakes environments such as automotive manufacturing and aerospace engineering.
Real-world experience highlights the significance of properly installing and maintaining lifting clamps. Regular inspection ensures that any wear or potential failure points are identified and addressed promptly. Maintenance of these clamps not only extends their lifespan but also ensures continuous operational trustworthiness. Equipment maintained with expert precision relays confidence across the entire operational chain, minimizing downtime and maximizing output.
sheet metal lifting clamps
Professionals using lifting clamps comprehend the delicate interplay between the tool’s mechanical prowess and human expertise. It is not enough to rely on high-quality equipment; operators must be trained thoroughly in the nuances of the clamps’ functionality. This dual emphasis on expert product knowledge and practical experience fortifies the authoritative use of lifting clamps in sheet metal handling.
The authenticity of experience is further emphasized by real-world scenarios where lifting clamps have excelled in accommodating unique challenges. Consider a scenario where the manufacturing plant transitions to a newer, lighter sheet metal alloy. Here, the versatility and adaptability of modern lifting clamps, together with an operator’s seasoned insights, ensure a seamless integration into existing workflows, testifying to their authoritative and trustworthy nature.
The interdependency between advanced lifting clamp technology and operator expertise is clear. This dynamic ensures safe, efficient, and precise handling of sheet metals—crucial to maintaining not only productivity but also the health and safety of personnel. Whether it’s ensuring a flawless finish on an automotive panel or a precise cut in construction materials, the role of these clamps is undeniable.
Through continuous innovation and unwavering adherence to safety standards, lifting clamps extend beyond mere instruments to vital components in the seamless, secure handling of sheet metal. Their role is an assurance of trustworthiness and expertise, a testament to both the devices’ engineering and the proficiency with which they are wielded. This synergy propels industries forward, building an unshakable foundation on the principles of safety, efficiency, and integrity.