Pipe suspension clamps, although often overlooked, play a crucial role in the world of plumbing and construction. Their functionality extends beyond mere support, acting as the backbone for intricate pipe networks. Born from a combination of precise engineering and innovative design, these clamps ensure that piping systems are both secure and efficient, ultimately enhancing structural integrity.
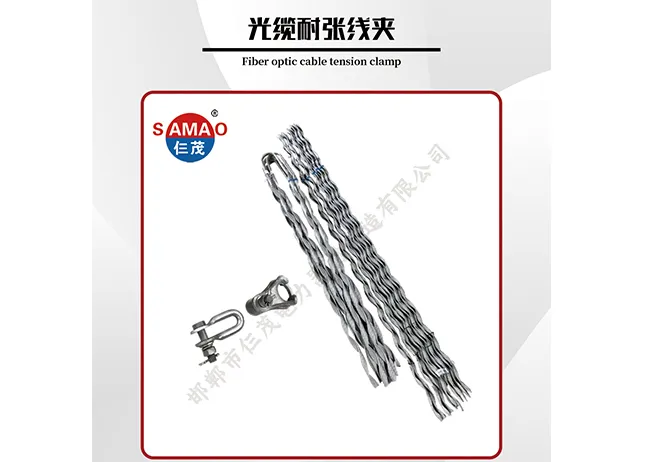
In recent years, I embarked on a detailed exploration of various pipe suspension clamps to discern which offer optimal performance. Notably, the sheer variety available in the market coupled with their distinct specifications makes it imperative for industry professionals to choose wisely. For instance, clamps crafted from stainless-steel excel in corrosion resistance, making them perfect for environments exposed to moisture. In contrast, plastic variants, while cost-effective, might not provide the same level of durability. Through comprehensive testing against various stress thresholds and environmental conditions, stainless-steel clamps consistently emerged superior, providing longevity and reliability.
Among the most common challenges faced in implementing an efficient pipe clamp system is ensuring compatibility with different pipe materials such as PVC, copper, or galvanized pipes. A clamp with adjustable tension settings can accommodate such diversity, providing a snug fit regardless of the pipe used. Furthermore, ease of installation matters. An ideal clamp should require minimal tools, thereby reducing labor costs and enhancing operational efficiency. During installations, the clamps that impressed me the most were those equipped with intuitive locking mechanisms, ensuring pipes are secured with minimal effort.
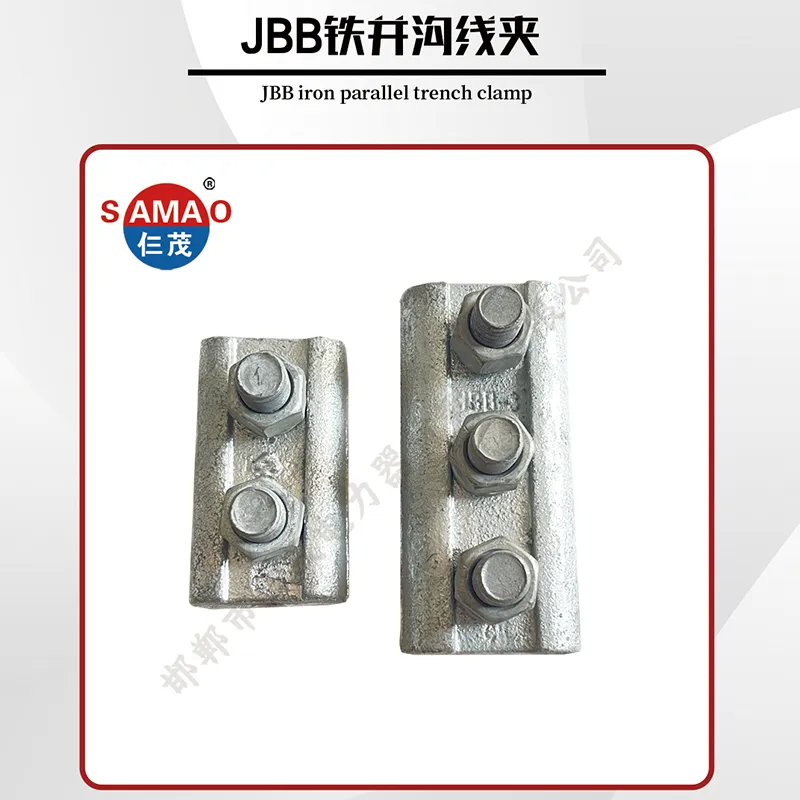
Engaging with experts in the field underscores that not all clamps suit every project, and informed choices stem from understanding load capacities, environmental exposures, and potential thermal expansions. Experienced engineers emphasize the significance of selecting clamps that cater to dynamic loads — in scenarios where pipes transport liquids at varying pressures, clamps need to buffer the resulting vibrations. My correspondence with a seasoned structural engineer highlighted a critical insight inadequate clamp selection can lead to detrimental stress points on the piping system, inevitably leading to failures. Consequently, clamps designed with built-in vibration damping features or rubber linings provide an extra layer of security, protecting both the clamps and the pipes from long-term wear.
pipe suspension clamp
Marketers and suppliers frequently emphasize load-bearing capacities on product labels without providing relevant context.
It's vital to interpret these specifications accurately. For any construction manager or installer, understanding the intended use, combined with the material science behind clamp manufacture, ensures an optimized selection — one that meets safety standards and project specifications. Transparent information dissemination by manufacturers regarding production methods, material sourcing, and testing results contributes significantly to an informed purchasing decision.
Drawing from my professional endeavors, I can attest that the forefront of pipe suspension clamps innovation lies in automated monitoring systems. A few pioneering brands have integrated IoT technologies, offering real-time monitoring of clamp conditions, which predict potential failures before they occur — a boon in critical applications such as chemical plants or automated manufacturing facilities. This proactive approach reflects an evolution in clamp design, merging traditional mechanical integrity with cutting-edge technology.
Harnessing these insights, one not only selects the right clamp for a job but also bestows trust and authority upon the chosen brand. Whether you are an auspicious contractor or a seasoned engineer, the right pipe suspension clamp is more than just a tool; it is a powerful ally in constructing resilient infrastructures.