Power cable manufacturing is a critical component in the burgeoning energy sector, bridging the gap between power generation and consumption. In a world increasingly dependent on electricity for both industrial and personal needs, the role of reliable and efficient power cables cannot be overstated. This article delves into the nuances of the power cable manufacturing industry, exploring the complexities and innovations that define this domain.
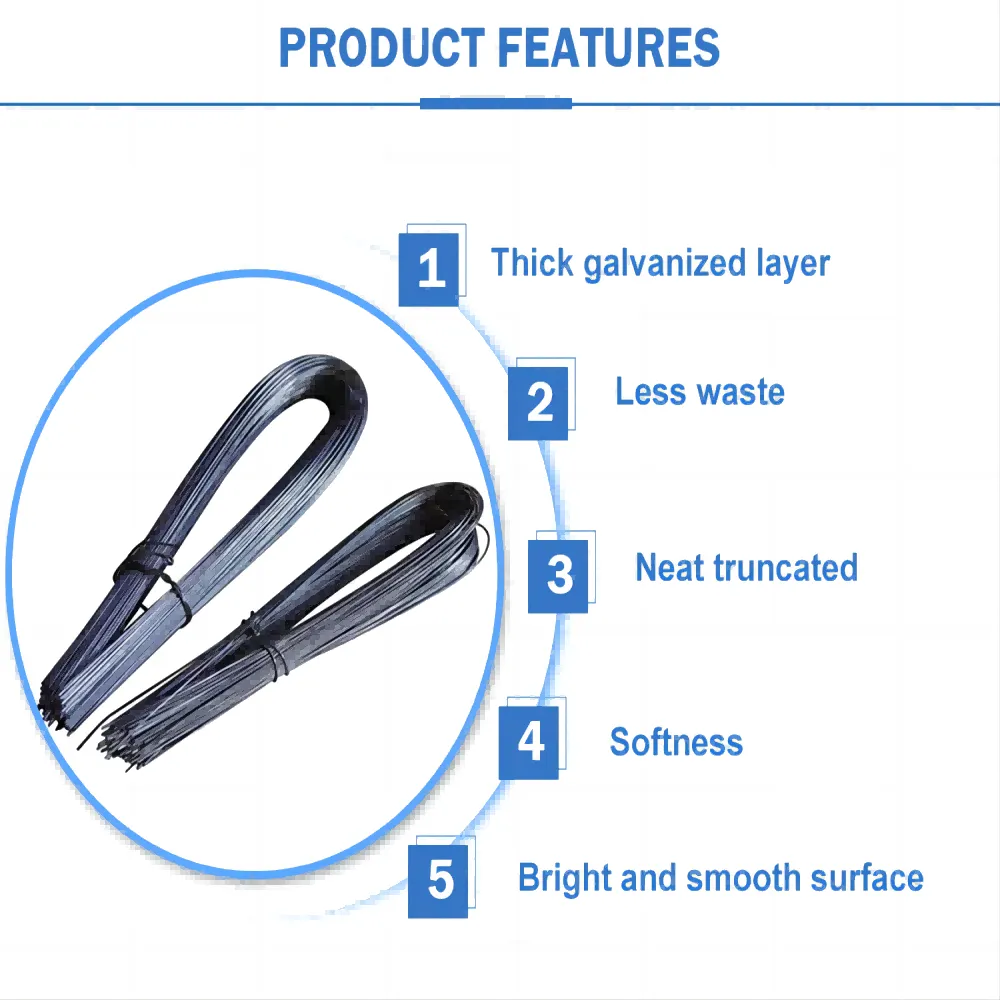
The process of power cable manufacturing is both intricate and precise, requiring a blend of advanced technology and skilled craftsmanship. At the heart of this process is the transformation of raw materials into durable, high-performing cables capable of withstanding environmental stresses and ensuring seamless electricity transmission. Top-tier manufacturers employ state-of-the-art machinery and rigorous testing protocols to achieve unparalleled quality standards.
One of the critical factors in manufacturing power cables is the selection of materials.
Copper and aluminum are the primary conductors used due to their excellent electrical properties. High-quality insulation materials, such as cross-linked polyethylene (XLPE) or ethylene propylene rubber (EPR), are employed to ensure the cables can withstand high voltages and thermal variations. Many factories are now investing in research and development to explore eco-friendly materials, aligning with global sustainability trends.
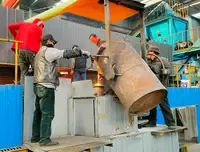
In terms of technological expertise, innovations such as superconducting cables are paving the way for more efficient power transmission. These cables have near-zero energy loss, significantly improving the overall efficiency of power networks. Furthermore, the integration of smart technologies within power cables allows for real-time monitoring and diagnostics, ensuring maintenance can be predictive rather than reactive.
Power line factory
The manufacturing process itself is a testament to industrial precision. Typically, it begins with wire drawing, where the chosen metal is drawn into thin strands under controlled conditions. This is followed by the stranding process, whereby these wires are twisted together to enhance flexibility and conductivity. The subsequent stages involve extrusion and vulcanization, where insulation materials are applied and heat-treated to ensure resilience and long-term performance.
Quality assurance is integral to the reputation and trustworthiness of a power cable manufacturer. Comprehensive testing is conducted at multiple stages of production, from raw material inspection to finished product evaluation. Tests include mechanical stress tests, thermal endurance assessments, and voltage resistance checks, all designed to simulate real-world conditions and ensure compliance with international standards.
Authoritativeness in this industry is often reflected through certifications and adherence to global standards, such as those set by the International Electrotechnical Commission (IEC) or the Institute of Electrical and Electronics Engineers (IEEE). Manufacturers that obtain these certifications are recognized for their commitment to quality and safety, building trust with consumers worldwide.
In conclusion, the power cable manufacturing industry is undergoing a transformative phase, driven by technological advancements and a growing emphasis on sustainability. The expertise required to navigate this industry is immense, with manufacturers needing to balance innovation with reliability and environmental responsibility. As demand for electricity continues to soar, so too will the need for robust, high-quality power cables, making this sector pivotal in the journey toward a more connected, energy-efficient world.