In the rapidly evolving world of technology, the role of well-engineered mechanical systems plays an essential part in ensuring operational efficiency. Among these systems, spring-loaded suspension devices have garnered attention for their versatility and efficiency. These devices, which are critical for reducing shock and maintaining stability, have found applications in various fields such as automotive engineering, industrial equipment, and even in consumer electronics. Understanding the intricacies of these devices is crucial for optimizing their performance and ensuring longevity.
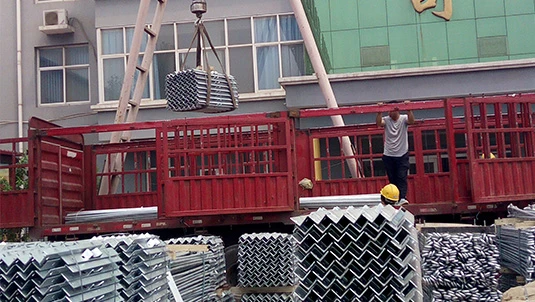
One of the key factors in the design of spring-loaded suspension devices is the material selection of the springs themselves. The choice of material affects not only the durability and weight of the system but also its ability to withstand various environmental conditions. Materials like stainless steel, titanium alloys, and composite materials are commonly used due to their high tensile strength and resistance to corrosion. This ensures that the devices can function reliably over extended periods without significant maintenance.
Beyond materials, the geometry of the spring itself is critical in defining the performance parameters of the suspension device. Engineers often utilize advanced simulation software to model different configurations and load scenarios. By optimizing parameters such as coil diameter, wire thickness, and the number of active coils, designers can tailor the spring to specific load-bearing requirements and dynamic response characteristics.
This precision engineering allows for the customization of devices to meet the specialized needs of different industries.
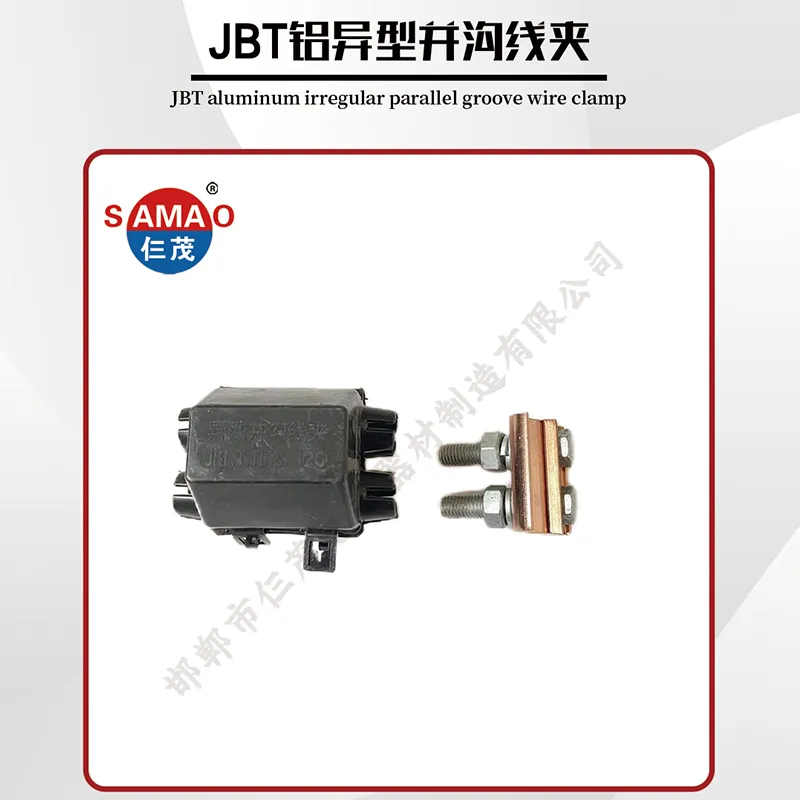
In practical applications, the effectiveness of spring-loaded suspension devices is not merely a function of their design but also how they are integrated into larger systems. In automotive applications, these devices contribute to ride comfort by mitigating the transmission of road irregularities to the vehicle’s chassis. Meanwhile, in industrial machinery, they diminish the transmission of vibrations to precision instruments, thereby enhancing accuracy and lifespan.
Spring holding of suspended equipment
Experience in the field has shown that regular maintenance and periodic testing are vital for the sustained performance of these devices. Over time, factors such as metal fatigue and environmental exposure can degrade the performance of the springs. Experts recommend employing predictive maintenance techniques, such as vibration analysis and ultrasonic testing, to preemptively identify potential issues before they result in system failures.
With a growing focus on sustainability, modern advancements in spring-loaded suspension technology are also exploring eco-friendly manufacturing practices. This includes the use of recyclable materials, and energy-efficient production processes. There is also an increasing interest in smart suspension systems that utilize sensors and active control systems to adapt to changing conditions dynamically. These innovations not only enhance the performance but also extend the service life of the devices, aligning with global sustainability goals.
In conclusion, spring-loaded suspension devices are indispensable components in numerous mechanical systems, providing critical support and shock absorption. Their design, material selection, and integration into broader systems require a nuanced understanding of both mechanical principles and practical application contexts. By adhering to best practices in materials science and mechanical engineering, and by incorporating cutting-edge technology and sustainable practices, these devices continue to evolve, ensuring high performance across a variety of applications. As industries continue to demand more efficient and sustainable solutions, the evolution of these devices is poised to play a pivotal role in meeting these needs.