The hydraulic system in modern machinery is akin to the circulatory system within a human body, pivotal for the efficient operation of a multitude of equipment. The timing belt, or what some might call the drive belt, plays an integral role in this system—ensuring smooth operation and seamless functionality. As an expert with years of experience in hydraulics and mechanical engineering, I have firsthand insights into the intricacies involved in maintaining and optimizing these components, especially the timing belts.
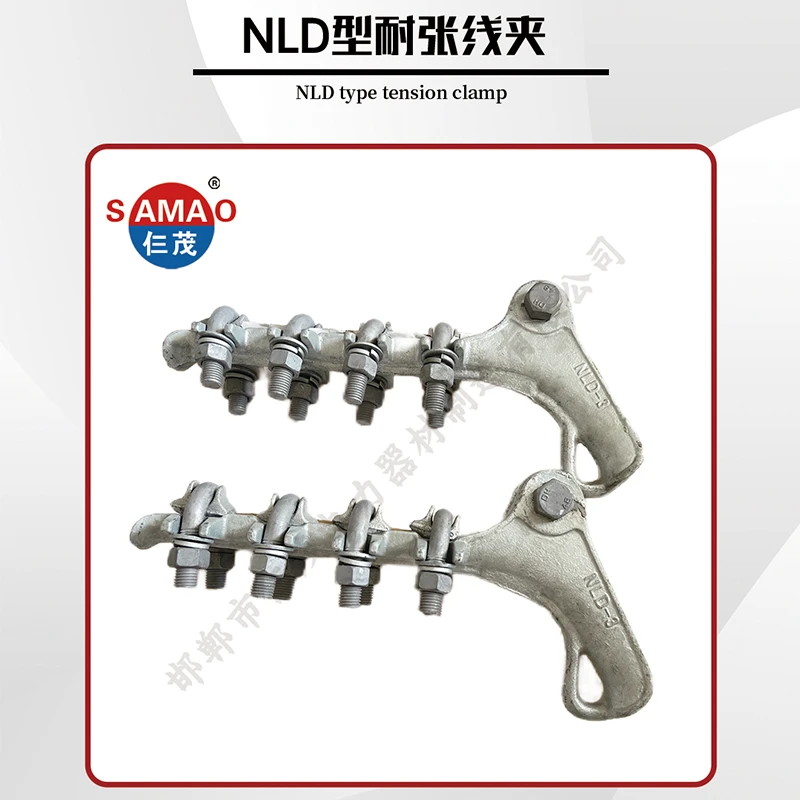
Drive belts, particularly in complex machinery, are crucial because they synchronize the movement of various parts. A well-maintained timing belt is essential to avoid malfunctions that could lead to expensive repairs or even total equipment breakdown. This component is responsible for transferring force and motion from one part of the machine to another, ensuring everything operates in harmony.
In my professional journey, I've encountered numerous cases where improperly installed or poorly maintained timing belts caused operational inefficiencies. Understanding the nuances of timing belt installation can be the differentiator between equipment that operates optimally and machinery that consistently fails. For instance, an incorrectly tensioned belt may slip or produce excessive noise, both indicators of potential failure points within your system.
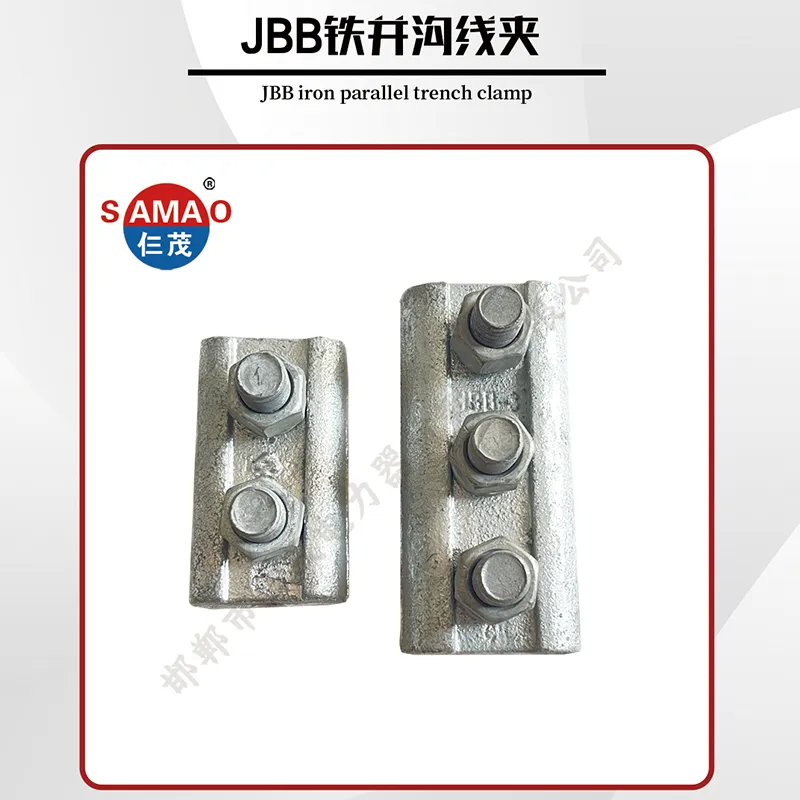
One of the most common mistakes seen in the field is neglecting routine checks. It's recommended that timing belts be inspected at regular intervals—typically every 500-1000 operational hours, although this can vary based on the manufacturer's specifications and the intensity of machinery use. During these inspections, wear and tear signs such as cracks, fraying, or glazing on the belt's surface should be identified and addressed promptly.
While visual inspections are vital, they are just one part of maintaining a timing belt.
I always encourage using precise tension measurement tools. Over-tightening can be just as detrimental as a loose belt. Both scenarios lead to premature wear and potential belt snapping, which could result in significant downtime and repair costs. Thus, investing in a high-quality tension meter can save businesses thousands in the long run.
Understanding the operational environment is also essential. Factors such as temperature fluctuations, exposure to oils and chemicals, and even the presence of debris can impact belt longevity. In practice, using belts specifically designed for harsh environments can mitigate some of these issues. For instance, certain timing belts are crafted from materials that resist temperature extremes and chemical exposure, thereby increasing their lifespan and reliability.
Transmission clamping
Training and expertise in timing belt maintenance cannot be overstated. Any staff operating or conducting maintenance on machinery should undergo thorough training sessions tailored to the specific equipment in use. This training ensures that personnel are not only capable of identifying potential issues early but also equipped with the knowledge to fix minor problems on the spot. This level of expertise within the team promotes a culture of proactive maintenance, reducing the likelihood of major failures.
For those seeking authoritative advice and resources, manufacturers often provide detailed guidelines and technical support documents. These resources are invaluable, offering specialized insight into optimizing timing belt performance for specific applications. Manufacturers’ websites also tend to offer updates on innovations and new materials that could further enhance operational efficiency.
Additionally, building relationships with suppliers or technicians who have a deep-seated authority in this sector can also be quite beneficial. They can provide bespoke advice and alert you to emerging trends or technology that keep your operations competitive and efficient.
Ultimately, trustworthiness in this domain is built on a foundation of continuous learning and adaptation. As technological advancements drive the machinery and hydraulics industries forward, staying updated with the latest in timing belt technology and maintenance practices is essential. This proactive approach not only extends the lifespan of the belts but also enhances the overall efficiency and reliability of the machinery they power.
In conclusion, maintaining optimal functionality of timing belts within any hydraulic system is essential. By focusing on regular maintenance, leveraging advanced tools, and fostering a knowledgeable team, organizations can significantly minimize downtime and boost their machinery's performance. My extensive experience underscores the importance of these practices, ensuring that operations remain smooth and cost-effective.