Understanding the intricacies of suspension clamping levels reveals their indispensable role in various industrial applications. These components, though often overlooked, significantly impact system efficiency, safety, and longevity.
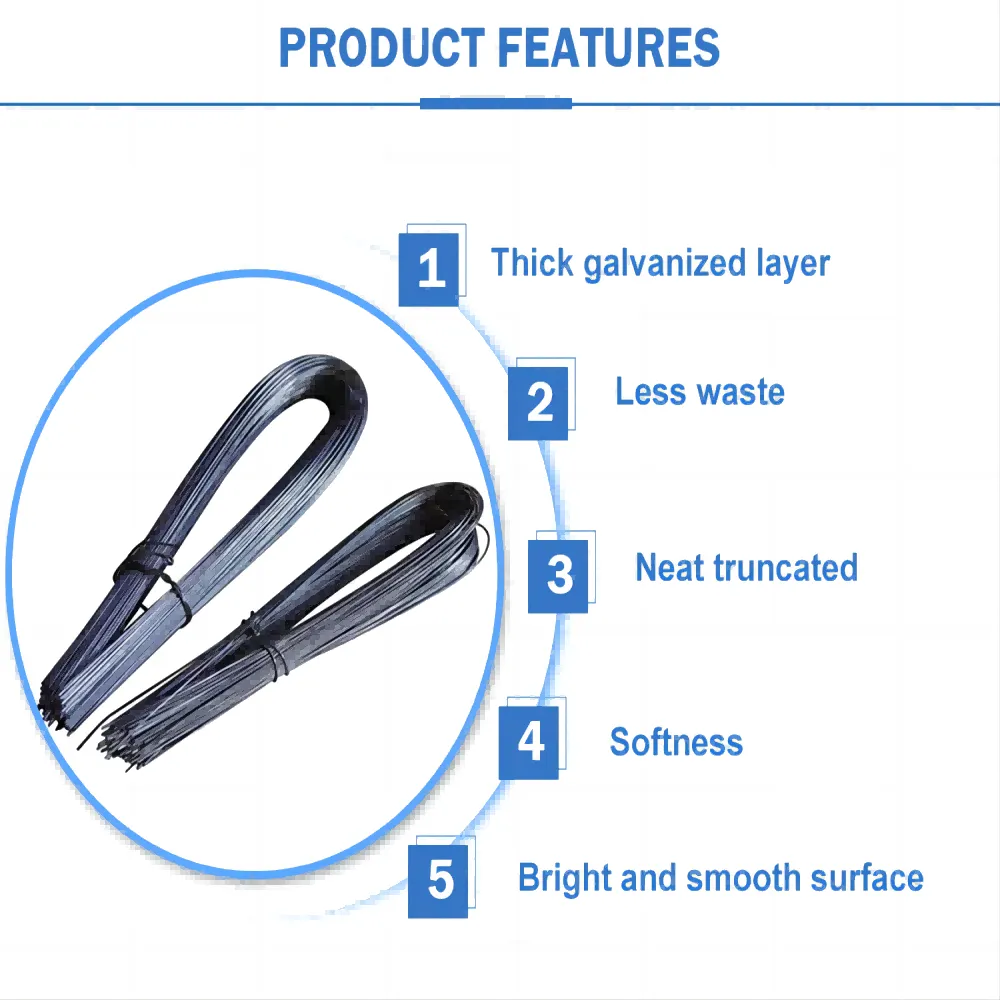
Suspension clamping systems serve as critical components in the management of cables, pipes, and other infrastructural elements. Their primary function is to secure these elements without causing damage or hindrance to their function. However,
understanding the correct suspension clamping level is pivotal. This level determines the force exerted by the clamp onto the cable or pipe, ensuring it is firm yet gentle enough to avoid wear and tear.
Industry professionals routinely emphasize the importance of selecting the appropriate clamping level, aligning it with the diameter and material of the conduit being secured. This not only safeguards against physical degradation but also mitigates the risk of operational downtime due to damage-induced failures.
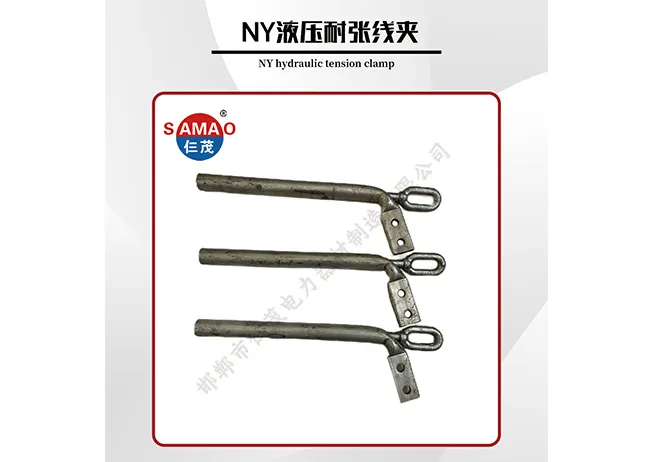
In terms of expertise, insights drawn from engineers and technicians who develop and implement suspension clamping systems underscore the necessity for precision. They highlight that inappropriate clamping can result in excessive pressure, leading to micro-cracking or complete structural failure over time. Conversely, insufficient clamping can allow for unnecessary movement, increasing wear and potential disconnection.
Adopting industry standards and relying on certified products further enhances the effectiveness of suspension clamping systems. These products undergo rigorous testing to ensure their reliability under various environmental conditions, including extreme temperatures, vibrations, and exposure to corrosive substances. This level of vetting reinforces their credibility and dependability in critical applications.
Level of clamping suspension
Real-world anecdotal experiences from seasoned professionals provide additional depth to understanding clamping systems. For instance, in high-stakes environments like offshore drilling or aerospace, the margin for error is minimal. Insights from these sectors reveal how precise calibration of clamping levels can mean the difference between operational success and catastrophic failure, thereby emphasizing trust in established practices and products.
As technology advances, smart clamping systems are emerging, integrating sensors to monitor pressure levels in real-time. This innovation allows for adjustments to be made automatically, thus maintaining optimal clamping pressure irrespective of external changes. Such advancements not only represent the pinnacle of engineering precision but also substantially bolster the trustworthiness of these systems.
Moreover, adopting these systems speaks volumes about a company's commitment to safety and efficiency. Demonstrating expertise through the implementation of the latest technologies reflects a dedication to maintaining cutting-edge operations, fostering trust amongst consumers and partners alike.
In conclusion, understanding and implementing the correct suspension clamping levels is crucial for optimizing industrial applications. By integrating professional expertise, rigorous testing, and real-time innovations, enterprises not only ensure system efficiency and safety but also establish themselves as authoritative and trustworthy entities in their respective fields. Such commitment to excellence and innovation in suspension clamping systems will invariably enhance operational success and sustainability.